All About Investment Casting for Aerospace Applications
Investment casting enables manufacturers to produce precision-engineered parts while minimizing material and energy waste. The word “investment” refers to the way that wax patterns are invested by a shell to create a vessel, which is then filled with molten metal.
Numerous aerospace components are produced via investment casting. Examples of these include:
- Air and fuel system parts
- Engine parts
- Hydraulic system parts
- Environment control system parts
- Landing control system parts
- Internal mechanical parts
- Interface controls for operators
- Cabin control system parts
Aerospace components must stand up to extreme weather conditions, pressures, and other factors that cause operational wear – thus, these parts require superior inherent durability. The consistency and precision of parts afforded by investment casting result in a significant increase in tensile strength. Creating aerospace parts through investment casting also ensures that interlocking parts can be matched up quickly and easily, preventing assembly errors that could otherwise lead to excessive wear or malfunction.
In this blog, we’ll offer insights into the investment casting process and explore its advantages for aerospace applications.
Key Investment Casting Benefits for Aerospace Components
Investment casting is well-suited for the production of aerospace components for the following reasons:
- Investment casting produces parts with the elaborate designs, thin walls, undercut holes, and slots that aerospace components frequently require.
- Parts made with investment casting will have a superior surface finish, reducing or eliminating the need for secondary machining.
- Investment casting produces parts of different sizes and weights.
Additional Investment Casting Benefits
Investment casting offers an abundance of benefits to those seeking high-quality custom aerospace parts. Not only does the process allow for exceptional quality control during every step of manufacturing, but it also:
- Ensures each part is tested via digital simulations and prototype test runs
- Leads to realized designs capable of operating through both mild and extreme conditions
- Facilitates detailed visual inspection of components
- Creates highly repeatable replicas through standardized procedures
- Forms components that meet all regulatory standards
Below are several points for consideration if you are evaluating investment casting for your aerospace component needs:
Diverse Alloys and Materials
Investment castings can be created from multiple alloys, resulting in end products that reap the benefits of several metals’ qualities at once. Alloys that are regularly employed within the aerospace industry include:
- Aluminum
- Stainless steels
- Titanium
- Super-alloys
Material selection is critical, as it will impact the unique physical properties that resulting parts will possess. These properties range from increased chemical and corrosion resistance, durability in the face of extreme temperatures, or other hazardous operating conditions.
Thorough Design Process
Designers rely on various software – such as CAD and CAM – and techniques when starting work on investment casting parts and prototypes. Successfully completing the steps of the initial design phase is critical to a component’s long-term performance. Prototyping, for example, allows designers to stress test parts and determine their operability in real-world settings.
Tight Tolerance Margins
Every measurement allows for some small level of deviation from set specifications, including thickness, diameter, and other related measurements. The more closely that resulting parts can adhere to an application’s measurement requirements, the better they will perform. Investment castings can be made to adhere to very tight tolerance margins, which leads to increased functionality of complex individual parts and complex systems containing multiple parts.
Thin and Streamlined Parts
Investment casting designs can be created to feature thin walls without the risk of losing structural integrity. Examples of these include undercuts, slots, threads, and more. Integrating critical assembly requirements into components is no issue for the investment casting process.
Working with Impro Industries for Your Investment Casting Needs
At Impro, we understand the critical importance of fabricating reliable and superior quality aerospace components. We take pride in crafting world-class investment casting components, using a great range of cutting-edge technology.
The Impro Team can provide you with:
- In-house rapid prototyping capabilities, tooling design & manufacturing to accelerate your time-to-market
- Software simulation process to examine the potential flaws
- Flexible manufacturing setup to accommodate low volumes, high mix
- Engineering and development support from initial collaboration
- In-house material testing, NDT, welding and heat treatment
- One-stop-shop solution throughout the entire product life cycle
- Worldwide logistics and warehouse facilities and sales offices to reduce the delivery time
For more information about investment casting and how it can support your aerospace operations, please contact us or check out our eBook, “Creating Aerospace Components with Investment Casting” linked below.
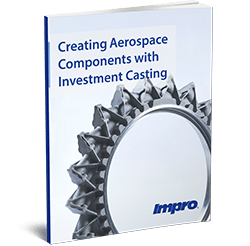
Download our eBook
Our Creating Aerospace Components with Investment Casting eBook is a guide to investment casting as it pertains to vehicles, tools and instruments in the aerospace industry.